QUALITY STANDARDS
At Raguvos Baldai, we leverage the latest technology alongside decades of industry experience to produce high-quality bathroom furniture and components for B2B clients. Our state-of-the-art manufacturing facilities are equipped with advanced machinery that prioritizes precision, efficiency, and sustainability.
We utilize robotic systems for key processes such as edging, sanding, and painting, which not only accelerate production but also minimize errors. This automation enhances the quality of our products while ensuring a safer and healthier work environment for our team.
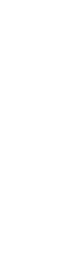
Facilities
Operating across three modern factories, Raguvos Baldai employs advanced equipment from renowned brands such as Cefla, Makor, and Homag to ensure precise production. We handle just-in-time, ready-to-order production, allowing us to efficiently manage large-scale orders while maintaining exceptional quality across all stages of the manufacturing process
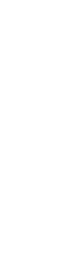
Painting and Finishing
Our Finishing Department utilizes modern equipment to achieve the highest standards of smoothness, aesthetics, and moisture resistance. A wide range of finishes is available, from high gloss to matte, with the ability to accommodate complex components and specific color requirements
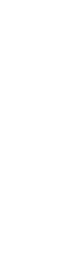
Automatic Edge Glazing Line
- Processes even surface furniture parts
- Line speed: 18 m/min
- Minimum component width: 80 mm
- Maximum component length: 2750 mm
- Standard edge radius: R3, R5, R8
- Custom radius available
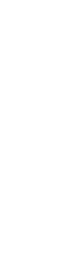
UV Roller Painting Line
- Ful automated process
- Painting speed: 13 m/min
- 100% UV-based mixture for painting and priming
- Emissions-free solvent
- Resistance to moisture and smooth, aesthetic finishes
- Environmentally friendly and human-safe process
Unlock superior quality in
bathroom furniture manufacturing
with us
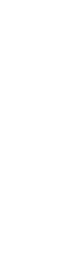
UV Priming and Painting Line
- Two-component UV paint formula
- Average painting speed: 125 m²/h
- Maximum moisture resistance
- 100% quality checks on all painted components
- Monthly capacity of 20,000 m²
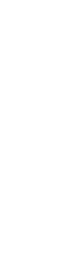
Cutting, Drilling, and Milling
Our cutting processes are driven by precision “Homag” machines that ensure accurate and efficient treatment of components. We use multifunctional CNC centers for drilling and milling, enabling precise production of furniture components. Our automated joining process guarantees consistent quality while speeding up production
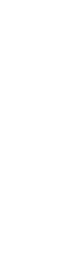
Edging and Durability
To enhance product longevity, especially in humid environments, we use specialized machinery for edging with polyurethane glue (PUR). This process ensures:
- Excellent resistance to humidity
- Aesthetic appearance with barely visible seams
- Durability across a wide temperature range (-30 to +140 °C)
- Easy maintenance and extended product life
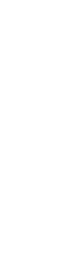
Assembly and Quality Control
Our assembly process adheres to a rigorous quality control system, ensuring that all furniture is assembled to the highest standards. Each unit is inspected twice during the assembly process, and we include labels with assembly details (date and assembler ID) to certify product quality
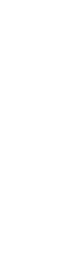
Packaging and Transportation
With years of experience, we have developed an optimal packaging system to ensure the safe delivery of our products. Our packaging is tailored to the size and weight of each unit, preventing damage during transportation. We also offer a specialized loading system for corporate orders, reinforcing pallets to guarantee secure transport and storage.
Our “door-to-door” transportation system ensures that your products reach their destination safely and efficiently.
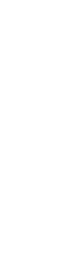
Sustainability and Material Handling
We work with certified suppliers of high-quality furniture components and ensure the proper storage of materials at optimal temperatures to maintain panel durability. Our commitment to sustainability is reflected in our closed-cycle production processes, minimizing waste and ensuring that every component is manufactured with the highest environmental standards in mind.